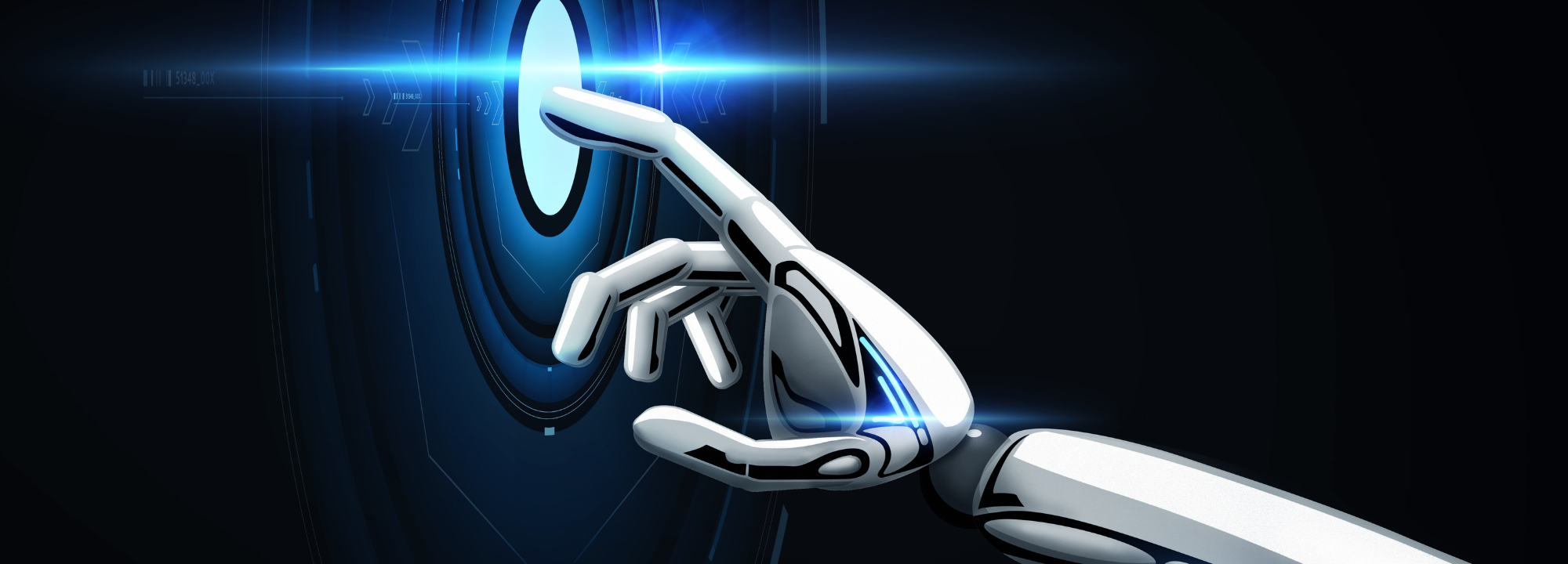
One tap to a mirror surface that even reflects your face
Stable production increases order volume, improves profit margins, and reduces costs at the same time!
Our mission is to contribute to our customers by improving the productivity and stability of fine hole polishing and adding maximum value to their products. We are also able to solve the following problems by introducing our equipment.
With the introduction of our equipment
Productivity has improved and overtime has been eliminated!
Stable production has been achieved and the defect rate has been improved!
Thanks to a technological breakthrough, we were able to commercialize the product!
It is easy to work with, so anyone can handle it, and it is very useful!
There are many companies that have solved this problem, even if it is currently difficult to do so.
In fact, to begin with,Physically unreasonable processing will not lead to the good results you are looking for.Because,This is because the optimal polishing method varies depending on the shape and material.Facts,One such difference is that we can do things that other companies cannot do, especially in the areas of “medical device parts” and “3D metal image products.
In fact, to begin with,
Physically unreasonable processing will not lead to the good results you are looking for.
Because,
This is because the optimal polishing method differs depending on the shape and material. In fact, we are able to do things that other companies cannot do, especially in the case of “medical device parts” and “3D metal image products.
\Talk to us now/
Technology and equipment that made the impossible possible
Our technology began with one company’s solution for fine hole polishing…
Since then, we have responded to all kinds of requests from the medical and industrial fields, where specifications are becoming more and more demanding every day, with our independently developed and patented technology and know-how.
We are capable of polishing not only medical equipment parts such as “medical metal pipes,” “injection needles for bio-cell injection,” “nozzles for analytical testing,” “catheter parts,” and “stent parts,” but also “fine hole flow paths in metal 3D modeling products,” especially “Ra 0.1” is possible.
In particular, polishing of “narrow-hole flow paths in metal 3D modeling products” is also possible with Ra0.1.
It is possible to polish even complexly shaped channels, channels and holes of 1mm or less, where gases and liquids flow!
It is capable of polishing not only medical device parts, but also “narrow channel channels in metal 3D modeling products” with Ra0.1, which enables polishing of complexly shaped channels, channels and holes of 1 mm or less for gas and liquid flow!
Patented technology developed in-house
Environmental Considerations and Efficiency
We have developed an “efficient” and “environmentally friendly” technology by using only “water” and “abrasives” in a single direction and using a circulating system.
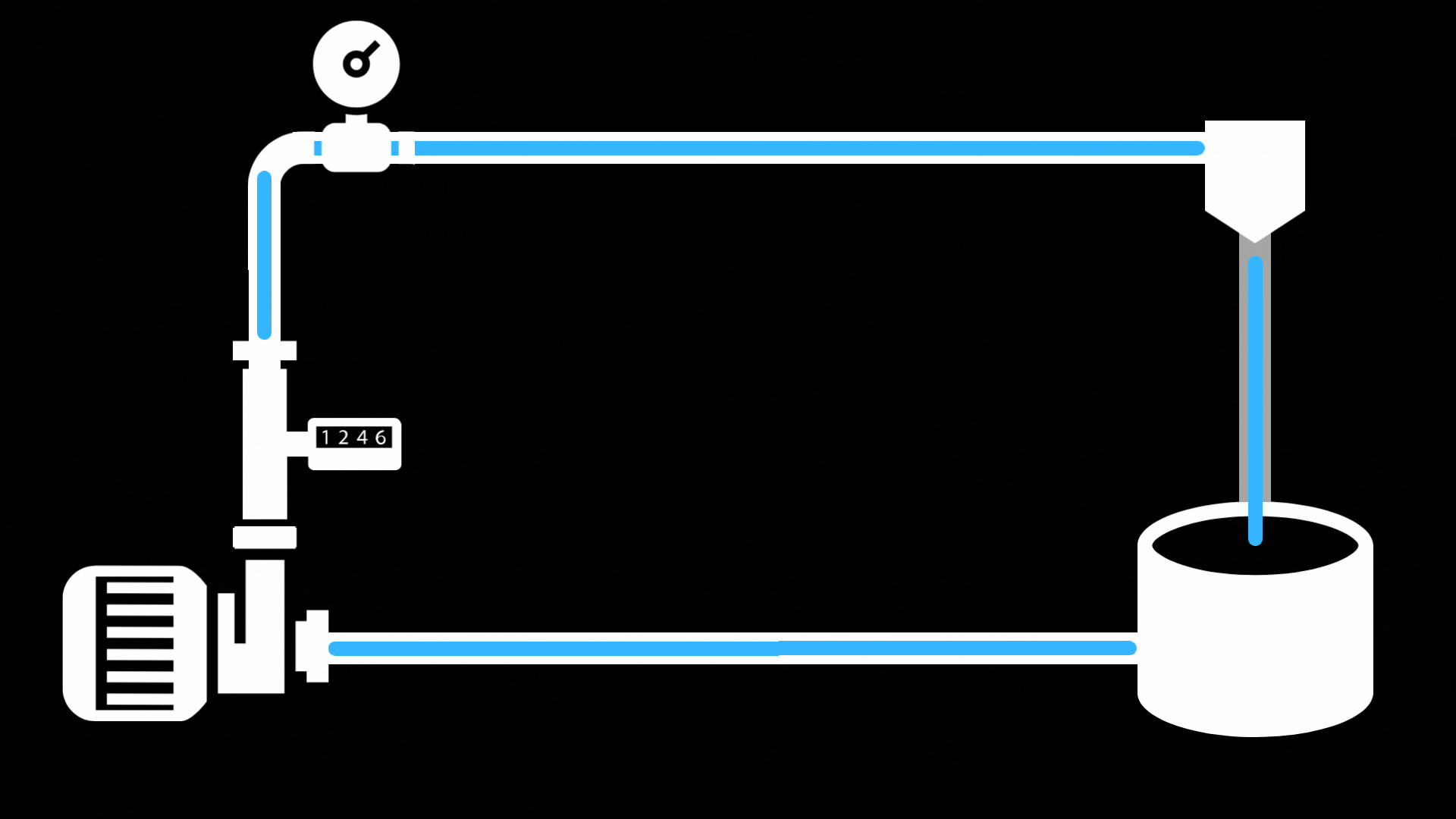
Polishing speed
The polishing speed is faster than other physical polishing methods because the abrasive particles hit the unevenness of the inner surface with the high-speed water flow.
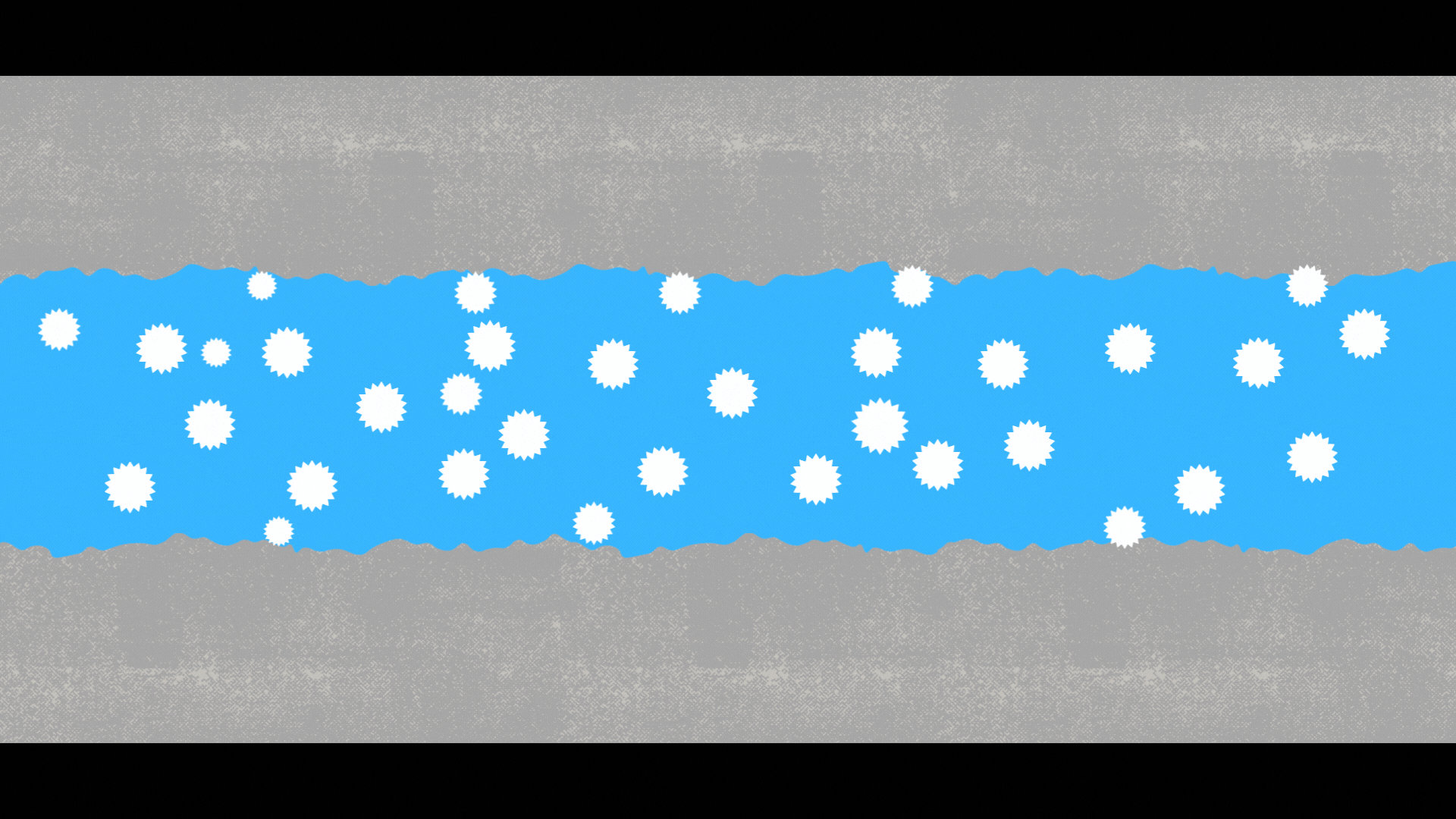
What is the difference between Argo and other companies?
What is fluid polishing?
Clay-like material, not fluid abrasive mixed with an abrasive.
Also, it is not magnetic fluid polishing using magnetism
Algo features a one-way circulation system
The single-circulation system eliminates the idle time for polishing and always produces a polishing action.
The reciprocating type, which is common in other companies, is…
Other companies’ reciprocating motion methods create idle grinding time by turning the grinding action on and off.
Amount of polishing for polishing time | Compatible types of work | Running cost | |
Fluid polishing (our company) | Large | Diverse materials, possible to polish from complex fluid channel to extremely small holes | Low cost by using low-price abrasive materials |
Polishing using magnetic force | Small | Possible to polish small holes, some shapes are incompatible | Abrasives are high cost |
Polishing using elastic fluid | Small | Not compatible for small holes | High price because diamonds are used |
Amount of polishing for polishing time | Compatible types of work | Running cost | |
our company | Large | Diverse materials, possible to polish from complex fluid channel to extremely small holes | Low cost by using low-price abrasive materials |
Polishing using magnetic force | Small | Possible to polish small holes, some shapes are incompatible | Abrasives are high cost |
Polishing using elastic fluid | Small | Not compatible for small holes | High price because diamonds are used |
Semi-custom in-house manufacturing equipment
Although the basic structure is the same, no two companies manufacture the same equipment, which is sold as the optimum “polishing solution” for each customer’s workpiece. It took 5 years of development to pursue “ease of use,” “reproducibility,” and “durability!
elite580 | |
---|---|
Processing Size: | Inner diameter/Up to Φ4 Overall length/Up to 1500mm (Special specifications are also acceptable) |
Number of pieces processed: | Pipe / up to 4 pieces 3D printer product / 1 piece ~ (special specifications also available) |
Corresponding material: | Almost all metals, cemented carbides, resins, etc. |
Dimensions: | 2200㎜×1600㎜×900㎜ (H x W x D) |
Weight: | 300Kg~ |
Power source: | 3-phase 200V |
Guarantee: | 1 year |
Grinding Results
Example of medical device pipe polishing
Before polishing
Ra0.736
After polishing
Ra0.07
Examples of polishing 3D metal modeling
Before polishing
Ra10
After polishing
Ra0.13
「Voice of the company that introduced the equipment」
「Voice of the company that introduced the equipment」
Flow of equipment installation and contract polishing
STEP1
Please contact us for a consultation!
+81 744-27-2800
(Japanese only)
STEP2
Hearing of issues
・Web interview
・Conference call
・In-home consultation
STEP3
Polishing Test
・Test Grinding
・Customer Evaluation
・Improvement of conditions
STEP4
Equipment delivery
STEP4
Contract processing
The cost of test polishing will be deducted from the price when the equipment is purchased!
Flow of equipment installation and contract polishing
STEP1
STEP2
Hearing of issues
STEP3
Polishing Test
STEP4
Equipment delivery
Contract Polishing
The cost of test polishing will be deducted from the price when the equipment is purchased!